6 tips and tricks to run and successfully maintain your Stratasys Fortus FDM machine
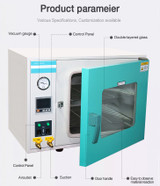
Every time one of your spools runs out or a build takes longer than expected and delays another build, you probably wonder how you can maximize the efficiency and lifespan of your material without sacrificing build quality. After more than 25 years in the 3D printing business, the people at Argyle Materials have figured out some handy ways to get more for your dollar and time out of each spool. Here are 6 of our favourite tips.
Tips To Run & Maintain Stratasys Fortus FDM Machine
- Number one is our most time-efficient practice that may often be underutilized – learning to use foundation sheet leftovers on your 3D printer. What does it mean to use foundation sheet leftovers? It means using the unused foundation space to expedite the time when you can get other builds running, allowing you to complete multiple jobs at once while using the same foundation sheet. When printing the calibration square, try to identify the areas where there will be space. Once you’ve identified those areas, figure out if the part you’re printing next will fit that site, and you can position it in that area. You can position through the control center or machine controls to fill in the empty space—the cardinal rule for builds: never start a small build in the center of your build tray or foundation.
- Tip number two here is more of a tip and is pretty obvious. Always use like for like materials when reusing a Fortus foundation sheet so the remants of a previous build don’t warp or curl at different oven temperatures and get in the way of the print head fro the next build. When combining builds on a single tray to use the leftover foundation space and maximize the $5 foundation sheet ensure that the next build is set to be made in that same material. ABS builds need to be with other ABS builds. The same goes for all FDM materials, ASA, Nylon, TPU, PC-ABS, PC and Ultem. Even with PC-ABS or polycarbonate ABS, you should avoid combining it with ABS as they run at different Fortus build chamber temperatures.
The following few tips have to do with extending the life of your material spools or Fortus canisters via temperature and moisture control.
- You may have asked yourself what temperature you’re supposed to dry your FDM spools? The answer is that it depends on the type of material. Spool drying is a technique we use to avoid or remove moisture buildup while a partially used canister or spool has sat on the shel. The first step to this process is drying them vertically. The vertical orientation of the spool increases surface area for drying and prevents the filament wrap from falling down and crossed over the feed wrap potentially causing the filament to cease (taping vertically also prevents spillage). After placing the spool vertically, we can use the printing temperature of the material to determine the drying temperature. Middle point FDM materials such as ABS, PC-ABS, ASA and spinoffs should be dried at around 65°C for 8 hours or more if they’re open or partial spools. Stratasys or Argyle Materials new spool / canister best practice is to dry at least 4 hours with the canister lid off before loading in the Fortus Model or Support material bays. When drying nylon materials lower the drying temperature to between 45°C and 55°C but increase the dwell time and dry for an extended period (24 hours or more). Ultem, which prints at the highest temperature, needs to be dried at 65°C to 75°C but no higher, or you run the risk of the spool itself warping. Drying options include oven is a DZF 6050 vaccum oven: DZF-6050 vacuum drying oven uses (zzkeda.com) also shown below. Commercial vacuum ovens allow for better temperature control while the vacuum accelerates the drying process and removes the most moisture.
- How are you supposed to store your partially used canisters between use? How are you supposed to store brand-new spools? The answer to both is low moisture environments. Used spools or partial spools should be kept standing up in bins with desiccant such as a silica gel or better yet in nitrogen cabinets for the inert atmosphere. Brand new FDM canisters from Stratasys or refill spools from still need to be stored in low moisture areas, just not necessarily moisture-resistant areas since both the OEM and Argyle ship the materials in sealed moisture resistant bags with desiccant.
- What temperature is best for storing your 3D printing material? 3D printing materials need to come up to temperature before being used. Storing material canisters or spools in a cold environment can result in longer wait times while you wait for your material to get to room temperature. Room temperature is the best temperature to store your spools. Spools warming up from the cold too quickly can result in warping of your 3D printed part or bubbles in the material. Keeping spools in an environment that is too hot can lead to similar warping issues and moisture issues. Frequently hotter air means more humidity which means more moisture that can be absorbed into your filament material spools and cause problems. Once a spool is opened or partially used, you want to store it in as stable an environment as possible, constant room temperature and constant low moisture level.
The final tip has to do with tips. Cleaning them, measuring their use, and generally avoiding tip breakage and build failures.
- Tip maintenance of your FDM machine is important for ensuring build quality and avoiding costly build failures. The odometer on the machine is appropriately named because it measures the distance in inches of filament printed by the tip installed on your FDM machine. Generally, you shouldn’t run your tips past 1000 inches in prints; the odometer will tell you when you’re getting close to this point. Between every build it’s essential to clean the exterior of the tips by cleaning the white ceramic heat shields of any debris. Polishing the heat shields with 600 to 1000 grit sand paper also helps prevent remnants from attaching to the heat shield and getting left behind in a model layer. Cleaning extends the lifespan of each tip and gives you time to check for damage and buildup and to check the odometer. If you’re at 950 inches and the next build will use 100 inches, it’s best to change it out for a new one than to run the risk of the tip failing and the build failing as a result. Tip storage is also an essential part of maintenance. If you’re changing out the ABS tip from to run say PC for example you should clean the tip and store it back in the delivery tube at a constant temperature. You can extend the life of the tip and decarbonize the melt chamber using the Purge Filament Argyle sells and found here: 3D Printing Tip Maintenance Products | Argyle Materials. This link will also take you to the page where we offer low cost replacement brushes and flickers. Regularly replacing both brushes and flickers on a Fortus will ensure any purge remnants are scrapped off and left in the Fortus waste bin rather than your 3D printed part.
Those are Argyle materials six tips and tricks for getting the most efficient usage out of your FDM machine, materials, and components.